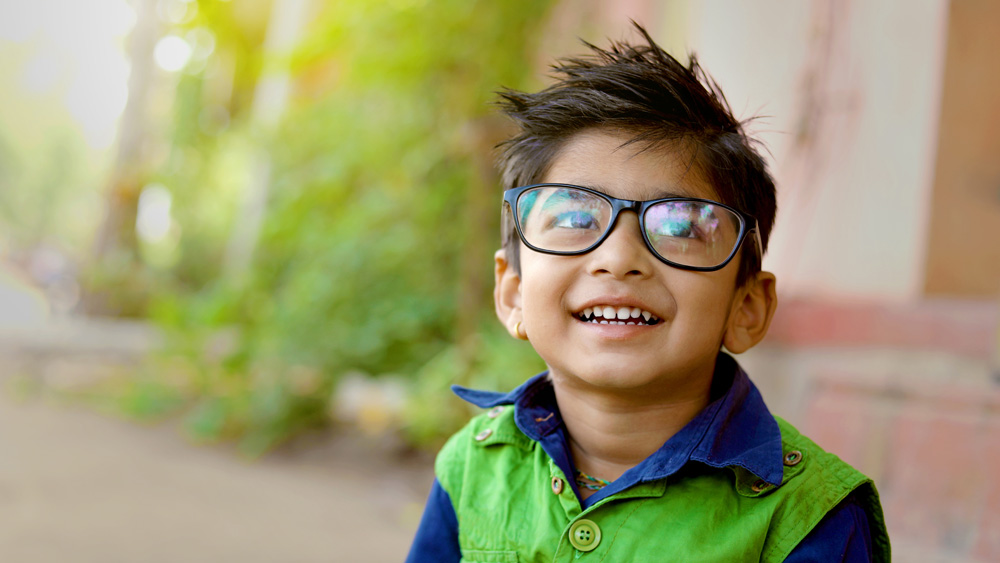
It’s that time of year when we start thinking about back to school and children’s eyewear.
And we do not think about kids’ eyewear without thinking about lens materials. The standard lens material for years has been polycarbonate. Seven years ago we had a newcomer to the lens material arena. In 2001, Trivex hit the optical marketplace.
Trivex was originally developed for the military, as visual armor. PPG Industries took the technology and adapted it for the optical industry. Trivex is a urethane-based pre-polymer. PPG named the material Trivex because of its three main performance properties. The three main properties are superior optics, ultra-lightweight, and extreme strength.
Trivex has a high abbe value. Abbe value is a measure of the dispersion or color distortion of light through a lens into its color elements. Abbe number can also be referred to as v-value. The higher the abbe number, the less dispersion, the lower the number, the more dispersion. Trivex has an abbe number of 43-45. This is significantly higher than polycarbonate. Polycarbonate’s abbe number is 30. Trivex has a very high level of light transmittance. The level is 91.4%. This is one of the highest levels of all lens materials. The high percentage is a factor that directly affects the brightness, clarity, and crispness of Trivex.
Trivex has a specific gravity of 1.11. Specific gravity is the weight in grams of one cubic centimeter of the material. Specific gravity is also referred to as density. The higher the number, the more dense, or heavy, a lens material is. Trivex has the lowest specific gravity of any commonly used lens material. This makes Trivex the lightest lens material. Trivex is 16% lighter than CR-39, 25% lighter than 1.66, and 8% lighter than polycarbonate! Trivex has a refractive index of 1.53. This allows for a thinner lens than a CR-39 lens. It can also be surfaced down to a center thickness of 1.0mm. This ability further reduces weight and thickness.
Trivex lenses are strong! They are as strong, or stronger than polycarbonate for impact resistance. Trivex is able to pass the ANSI Z87.1 High Velocity Impact Test. This test is a requirement for safety lenses. The lens must have a center/edge thickness of 2.0mm. The test consists of a mounted lens being subjected to a ¼-inch steel pellet being hurled at the lens at a velocity of 150ft per second. The FDA also requires lenses to be impact resistant. Their test consists of a 5/8 inch steel ball being dropped from a height of 50 inches onto a lens. Trivex not only passes the test at 2.0mm center thickness, it can even pass the test at a center thickness of 1.0mm. That is tough!
Lenses made from Trivex are very chemical resistant. They are even resistant to acetone. Polycarbonate is not resistant to acetone. Under normal conditions, Trivex is resistant to most commonly used household and optical cleaners and solvents. Cleaners such as Windex and alcohol are safe to use on Trivex.
Trivex lenses do not have the internal stress that is associated with most polycarbonate lenses. This is due to the way Trivex lenses are manufactured. Internal stress can cause lens breakage and is often referred to as birefringence. Birefringence can blur vision. The lack of internal stress makes Trivex a perfect choice for drilled and grooved rimless. Trivex does not crack around drill holes like polycarbonate. These cracks are often called “spider cracks.” Lenses in a drill mount sometimes experience hole elongation. This is due to the flexing and stress that happens to the lens. This can cause lenses to become loose and cause the frame to get out of adjustment. Trivex lenses retain their shape and are not subject to hole elongation.
Trivex lenses provide 100% UV blockage of both UV-A and UV-B radiation. This is inherent in the lens material. Trivex lenses are also very scratch resistant. This is especially important when comparing Trivex and polycarbonate for kids. I have read some literature that puts Trivex’s scratch resistance at twice that of polycarbonate!